How to Choose the Right Type of Rubber?
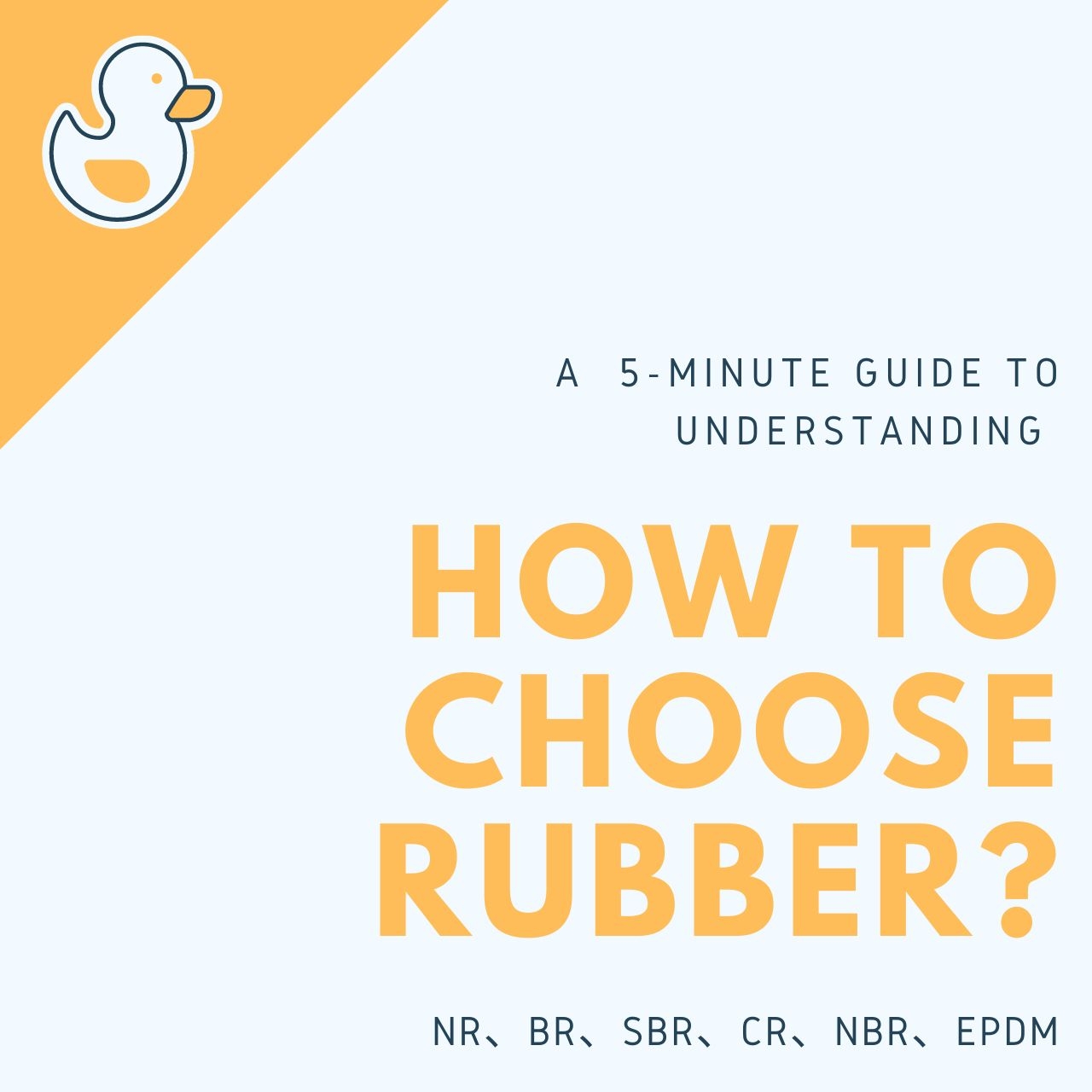
Apart from NR, which is natural rubber, BR, SBR, CR, NBR, and EPDM are all synthetic rubbers.
NR (Natural Rubber)
Composition
Natural Rubber (NR) is derived from the latex of rubber trees, primarily consisting of polyisoprene. The main sources globally are Hevea brasiliensis and Congo rubber. After being extracted from the rubber tree, NR requires vulcanization through commercial processing before it can be applied to various products.
Structure
The structure of NR is C5H8, linked into long-chain polymers through 1,4-addition reactions. Its chemical structure can be represented as:
Advantages
- High rebound
- Wear-resistant
- Flexibility
- Tear resistance
- Water resistance
- Low-temperature performance
- Extremely high elongation
Disadvantages
- Poor acid resistance
- Poor oil resistance, prone to swelling and degradation upon oil contact
- Not suitable for UV resistance
- Ozone sensitivity
- Poor heat resistance, performance declines at high temperatures, potentially leading to brittleness over time
- Emits an unpleasant odor if stored for a long time
Suitable Temperature Range
NR is suitable for temperatures ranging from -50°C to +80°C.
Main Applications
Large vehicle tires, shoe soles, industrial hoses, and vibration damping materials.
BR (Butadiene Rubber)
Composition and Structure
Butadiene Rubber (BR) is a synthetic rubber polymerized from butadiene monomers, primarily consisting of polybutadiene. Its chemical structure is as follows:
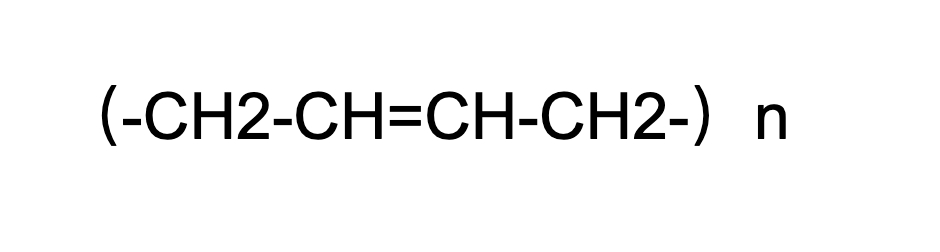
Advantages
- High elasticity
- High wear resistance
- Fatigue resistance
- Tear resistance
- Low-temperature resistance: BR remains flexible and doesn't become brittle in cold environments.
Disadvantages
- Poor oil resistance
- Similar to NR, BR is not heat-resistant and can degrade under prolonged exposure to UV and ozone, though it is better than NR and SBR.
Suitable Temperature Range
BR is suitable for temperatures ranging from -55°C to +100°C.
Main Applications
Truck tire treads and sidewalls, shoe soles, hoses, gaskets, and sports equipment.
SBR (Styrene-Butadiene Rubber)
Composition and Structure
SBR is a copolymer of styrene (Ph-CH=CH2) and butadiene. Typically, styrene content ranges between 23% and 30%, with the remainder being butadiene. The structural formulae are:
- Styrene: Ph-CH=CH2
- Butadiene: CH2=CH-CH=CH2
Advantages
- High strength: SBR has good elasticity and strength, making it highly wear-resistant. It is also more resistant to oxidation and ozone than NR, thus more durable.
- Easy to process: SBR has notable processing advantages, including lower costs, good mixing performance, stable vulcanization properties, and a wide processing range.
Disadvantages
- Poor oil resistance: Like NR, SBR's oil resistance is poor, prone to swelling and degradation upon oil contact.
- Lower elasticity and adhesion compared to NR, with potential hardening at high temperatures.
Suitable Temperature Range
SBR is suitable for temperatures ranging from -40°C to +100°C.
Main Applications
Tires, industrial seals, gaskets, and shoe soles.
CR (Chloroprene Rubber)
Composition and Structure
Chloroprene Rubber, also known as Neoprene, is a synthetic rubber polymerized from chloroprene. Its structural formula is:
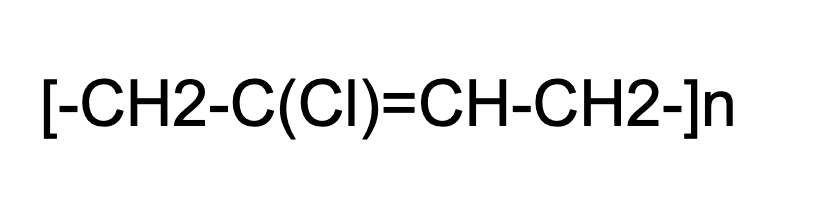
Advantages
- Excellent oil, water, and chemical resistance
- Resistant to oils, fuels, solvents, and various chemicals, making it more suitable for environments involving oil and chemicals compared to NR and SBR.
- Resistant to ozone and UV, not prone to aging.
- Flame resistance: CR has inherent flame retardant properties, suitable for applications requiring fire resistance, such as cable sheathing.
Disadvantages
- Higher cost, making it less suitable for cost-sensitive applications.
- More challenging to process.
- Inferior low-temperature performance compared to NR, BR, and SBR.
Suitable Temperature Range
CR is suitable for temperatures ranging from -40°C to +120°C.
Main Applications
Cable sheathing, wetsuits, industrial hoses, seals, and protective gloves.
NBR (Nitrile Butadiene Rubber)
Composition and Structure
Nitrile Butadiene Rubber (NBR) is a synthetic rubber copolymerized from butadiene (Butadiene) and acrylonitrile (2-propenenitrile). The structural units are:
- [−CH2−CH=CH−CH2−]n (butadiene part)
- [−CH2−CH(CN)−]m (acrylonitrile part), where CN represents the nitrile group.
Advantages
- Oil resistance: Excellent resistance to oils, fuels, and chemicals, especially petroleum-based products.
- Good wear resistance, tear resistance, and aging resistance, with some resistance to sunlight and ozone.
- Better heat resistance than NR, BR, and SBR, though inferior to CR.
Disadvantages
- Limited low-temperature performance: NBR may lose flexibility and elasticity in cold environments.
- Absorbs water: NBR has some water absorption, potentially affecting its performance in humid environments.
Suitable Temperature Range
NBR is suitable for temperatures ranging from -30°C to +120°C.
Main Applications
Sealing elements, oil-resistant hoses, fuel tank linings, and industrial gloves.
EPDM (Ethylene Propylene Diene Monomer)
Composition and Structure
EPDM is a synthetic rubber copolymerized from ethylene (Ethylene), propylene (Propylene), and a small amount of a third monomer (typically a diene such as ethylidene norbornene or 1,4-hexadiene). Its main components are ethylene and propylene, with the third monomer introducing double bonds for vulcanization.
Advantages
- Excellent aging resistance: Highly resistant to UV, ozone, and acid rain, not prone to aging.
- Heat, chemical, and electrical insulation resistance: Ideal for electrical applications. Also maintains good elasticity over a wide temperature range.
Disadvantages
- Poor oil resistance: Not suitable for environments involving oils and non-polar solvents.
- Difficult to process: Requires special formulations and processes to improve flow and adhesion.
- Higher cost: More expensive compared to some other synthetic rubbers.
Suitable Temperature Range
EPDM is suitable for temperatures ranging from -55°C to +150°C.
Main Applications
Automotive sealing components (such as door and window seals, cooling system hoses)
Electrical insulation materials (such as cable sheathing and high-voltage insulation)
Building waterproofing materials (such as roofing membranes and wall waterproofing materials).
Comparison of Properties of Six Types of Rubber Materials
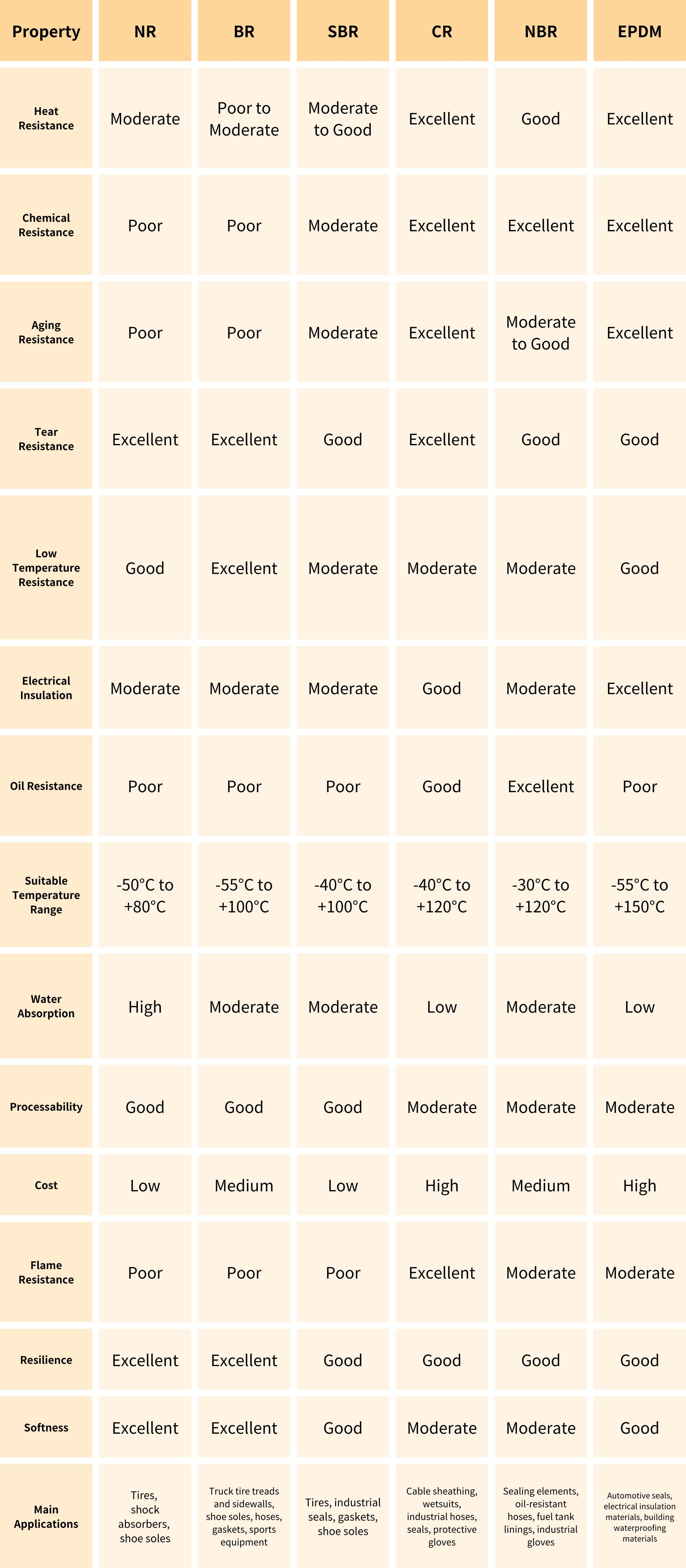
Our Expertise
If you have any questions about the types of rubber and their applications, please feel free to contact us by email or phone for further inquiries. With over 40 years of research and manufacturing experience, we will promptly provide you with a satisfactory response.