Understanding Sponge Rubber: A Quick 5-Minute Guide
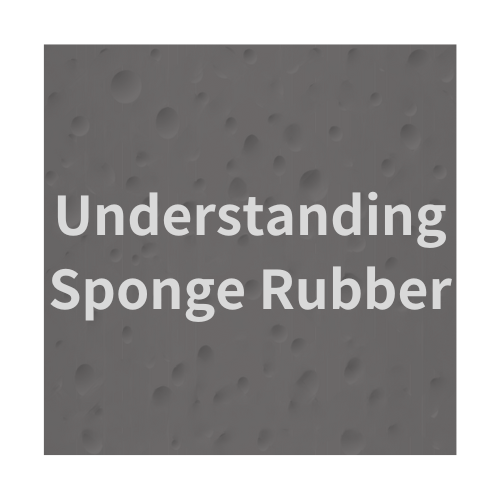
What is Sponge Rubber?
Sponge rubber is a product made through the vulcanization of rubber, featuring characteristics such as lightweight, porous structure, elasticity, thermal insulation, shock absorption, and soundproofing. It is widely used and commonly seen in various applications.
All types of rubber can be used to produce sponge rubber, typically chosen based on the specific properties required. For example, general sponge rubber can be made from natural rubber (NR) or styrene-butadiene rubber (SBR). For oil resistance, chloroprene rubber (CR) or nitrile rubber (NBR) can be used, and for fire resistance, CR is a suitable choice. (For specific needs, please feel free to contact us.)
How is Sponge Rubber Made?
The production of sponge rubber involves three processes: mixing, foaming, and vulcanization. First, foaming agents are added to the raw material mixture. Through heating or chemical reactions, the foaming agent releases gases, forming a porous structure. Finally, the material is molded and vulcanized in a mold to achieve the desired shape and properties.
Advantages
Unlike solid rubber, sponge rubber contains numerous air pockets within its structure, making it lightweight and soft. Its low density also makes it easier to transport. Due to its porous structure, sponge rubber offers excellent soundproofing, thermal insulation, and shock absorption.
Disadvantages
Due to its porous structure, sponge rubber has lower mechanical strength and wear resistance compared to solid rubber. Open-cell sponge rubber tends to absorb water, so for applications requiring waterproof performance, closed-cell sponge rubber is recommended.
Main Applications
Sponge rubber is commonly used in products such as sealing strips, soundproof mats, mouse pads, and pipe insulation sleeves.